SMT Assembly
Assembly of the latest generation SMD components
EES is able to assemble the latest generation SMT (Surface Mount Technology) components (μBGA, Fine Pitch, 0201, 01005, CSP) thanks to the use of two 100.000CPH production lines consisting of:
five Pick & Place machines (MY200DX & MY100SXe, i-pulse M2 & i-pulse M4e & i-pulse M1P)
two screen printing machines with visual inspection (VERSAPRINT S1, SP200AVI)
an in-line forced convection oven with 24 zones with air and nitrogen cooling (FL-VP1060N)
a Vapor-Phase Soldering System (ASSCON VP800).

The Machines
Mycronic line: My200DX+My100SXe
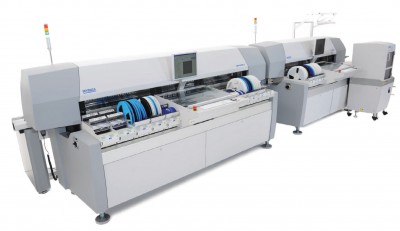
New generation Pick & Place machines
High performance flexible machines for speed and precision that allow the assembly of latest generation components (01005, 0201, fine-pitch, μBGA). The line has a loading capacity equal to 304 feeder + 32 JEDEC trays and a total speed of 64 thousand components / h which allows production and pre-production to be carried out in addition to prototyping thanks to the flexibility of the “agilis” system. The Ecr’s Mycronic machines boast an electrical test that elevates the control of components such as diodes, resistors, inductors and capacitors, not only from the visual point of view and of the coil feeder association (traciability system), but to a real measure of the nominal value of the component before placement.
i-Pulse Line: M2+M1plus+M4e

Pick & Place machines
The I-Pulse line boasts a strong feeder capacity (380 feeder + Tray Feeder with a capacity of 40 trays) which allows to mount boards with many types of SMD components with just one machine load. Reliable Japanese machines with a rated speed of 66,000 CPH. EES has chosen to use the Trolley load system in order to be able to load the machine off-line in order to accurately control the components and work in masked time in order not to weigh down the start and transfer to customers competitive costs.
The first feature of the MYCRONIC line is setup quickness. In fact, the Agilis intelligent loaders and the rapid assembly of data for assembly (from CAD, with the aid of Moror and MYCenter’s Valor Process Preparation) make it the ideal machine to make rapid prototyping, but not only, in fact with a production capacity of 64,000 CPH we are able to offer fast service even for production, guaranteeing precision (35 μm, 0.09 °) and repeatability of the process (21 μm, 0.05 °) that characterize the quality of EES products. In addition, the intelligent chargers make it possible to offer a “traciability” of the components that, with the help of the company MRP, provide total traceability (component traceability + process traceability).
Even though with different characteristics, which make them more suitable for standard assembly, the three I-PULSE machines are also synonymous with precision, reliability and repeatability.
The I-Pulse line that includes M1P + M2 + M4e has been designed to have a strong feeder capacity (380 feeder + Tray Feeder with 40 trays capacity) and to be able to mount boards with many types of SMD components with just one machine load that to make the rated speed (Rated Speed) equal to 66,000 CPH very close to the actual speed.
Another highlight of the smt line is undoubtedly the Versaprint S1 silkscreen by ERSA, which thanks to the scanner and the continuous pressure control of the squeegee guarantees 100% control of the process (control of the dough on the board and the cleaning of the plate, activating automatic washes). Moreover the precision of ± 25 μm @ 6 Sigma allows to have a highly repeatable serigraphy even on steps (pitch) 0.2mm.
In support of ERSAS we have the Speedprint SP210avi silk-screen, today it is used for machining operations that do not involve technologies that are not excessively strong.
Finally, EES has recently decided to invest in the Vapour-Phase Soldering System technology, which guarantees excellent temperature uniformity, focusing on the ASSCON VP800 oven. Vaphour Phase welding is the best technology to weld complex components such as BGA, QFP, QFN, POP etc, on densely populated boards with a wide variety of components.
Moreover, the Vapor Phase welding is very useful in the welding of devices where it is necessary to dissipate power (for example power LED diodes, D2PACK OR D3PACK) in fact the presence of Void, extremely dangerous in power circuits, with welding in Vapor Phase technology it reduces a lot.
Furthermore, the absence of oxygen during the recasting phase reduces oxidation problems.